

It is difficult for people to travel at high speed under extreme load, but robots can do so with the help of technology. Ultra-high-speed conveying technology assists high-efficiency assembly in 54 seconds/unit It is of innovative and advanced significance to have achieved a high automation rate, high production efficiency, high production quality and high flexibility of automatic assembly.
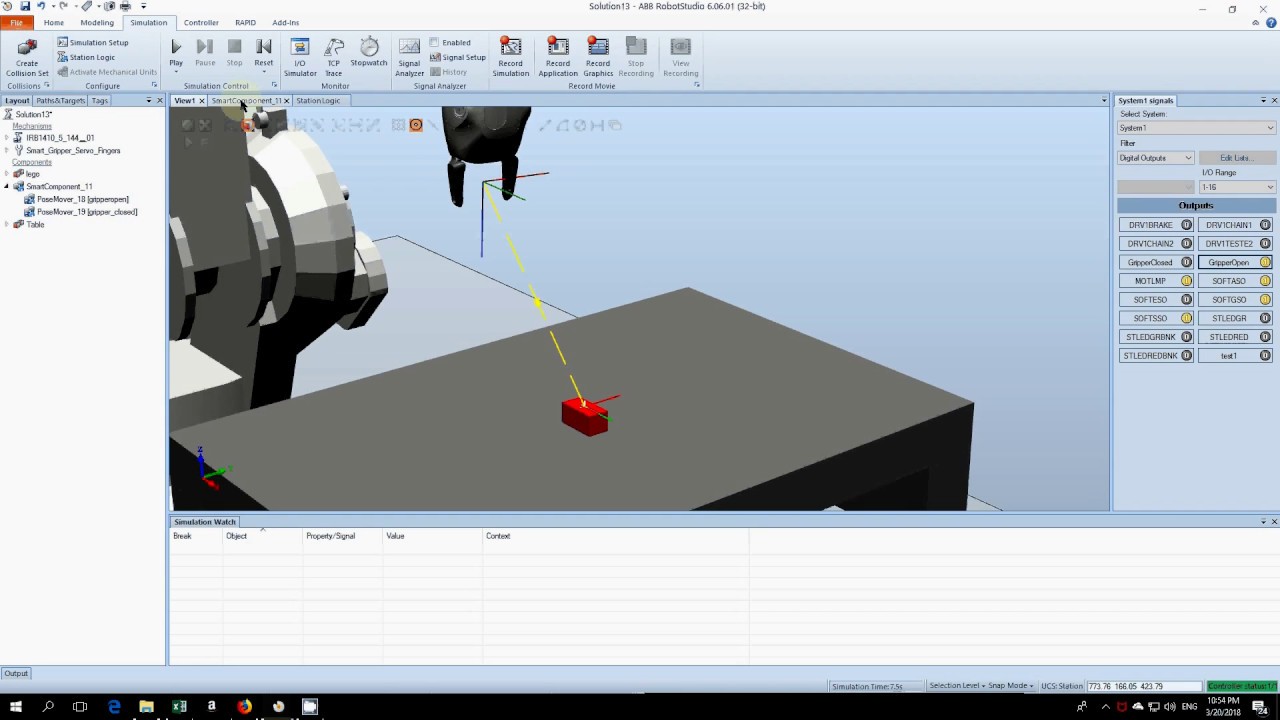
The entire line is fully automated by NC fixtures, and the shuttle system is used for body conveying, thus realizing the automatic assembly for the four doors, engine hood, trunk lid, and rear bumper in the takt time of 54 second/unit, automatic tightening of 64 screws, 4-second station conveying, and mixed line production for 8 models, with an annual production capacity of 200,000 units. The production line includes processes such as automatic grabbing from the EMS line in the air, automatic calibration, gap measurement, visual guidance, automatic tightening assembly, quality monitoring, and torque monitoring, and deeply integrates intelligent elements such as laser and binocular vision, automatic tightening system, information monitoring system, flexible NC, high-speed conveying, and intelligent IoT. Adopting all-round high-tech automation schemes-"Intelligent Visual Guidance Technology", "Intelligent Tightening Technology" and "Intelligent Quality Control Technology", with many core technologies reaching the international advanced level, the assembly line belongs to the model line case of intelligent manufacturing industry. This time, Risong Technology launched the leading automatic, intelligent and flexible door/hood/lid production line and took the lead in mass production. The body-in-white door/hood/lid production line is the production line with the most challenging automatic integration in the automotive field. This case promotes the intelligent development of the automotive industry, ensures a sustainable consumption and production mode, and promotes inclusive and sustainable industrial development by innovating manufacturing technology.

Youtube abb robotstudio mush brain manual#
In this case, due to the introduction of the door/hood/lid assembly and adjustment line, the full automatic assembly has been realized for the four doors, engine hood, trunk lid, bumpers, and bolts in the vehicle, thus achieving the goal of changing about 80 production workers from heavy manual laborers to skilled operators, and reduced the labor cost of the production enterprise by about RMB 15.6 million every year. You will find the package details on the ISR webpage.
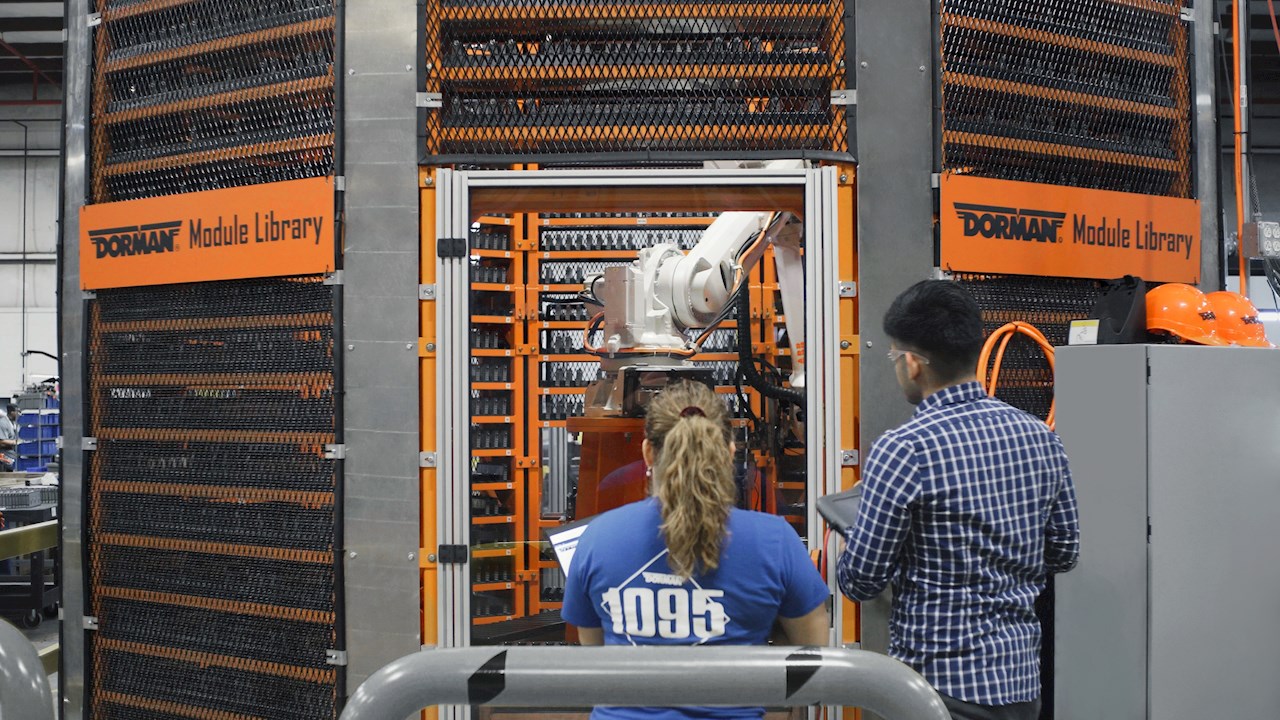
Please follow the instructions on the ISR webpage.ĭeadline for the submission of abstracts: FebruISR 2022 - Business TrackĪfter a successful kick-off during the ISR 2020 virtual conference, ISR will continue to offer an attractive package deal to showcase your brand in the major digital event during the “week of automatica”. Call for PapersĪll interested authors are now invited to submit their abstracts for the upcoming ISR 2022. The special session for the IERA Award finalists rounds up the conference program. The Business Track will offer invited speakers from the industry the opportunity to present current product developments. Selected conference topics include Modeling, Planning and Control, as well as Components and Technologies or Future Industrial and Service Robotics Applications. In two conference tracks and a poster session over two days, the ISR Europe 2022 will offer an insight into state-of-the-art robot technologies to participants from both industry and research. ISR Europe 2022 takes place parallel to the Automatica exhibition (June 21-24, 2022.) The 54th International Symposium on Robotics – ISR Europe 2022 will be held again in Munich, Germany on June 20-21, 2022.
